Understanding The ATL Chemical Fire: Causes, Impacts, And Lessons Learned
On a seemingly ordinary day, a massive fire erupted at the ATL chemical facility, sending shockwaves through the surrounding community and raising alarms about the potential risks associated with chemical plants. This incident not only disrupted the lives of thousands but also highlighted the urgent need for stricter safety protocols and better emergency preparedness. As flames engulfed the facility, emergency services worked tirelessly to contain the blaze, while residents were evacuated to safer locations. The event quickly gained national attention, sparking debates about industrial regulations, community safety, and environmental protection. In the aftermath of the ATL chemical fire, questions arose about how such a disaster could occur in the first place. Investigations revealed that a combination of equipment failure, inadequate safety measures, and human error contributed to the catastrophe. While the immediate focus was on containing the fire and ensuring public safety, long-term concerns about air and water contamination began to emerge. Toxic fumes released during the fire posed significant health risks to nearby residents, prompting authorities to issue warnings about exposure. The incident served as a wake-up call for both industry leaders and policymakers, underscoring the importance of proactive measures to prevent similar disasters in the future. As the community begins to rebuild and recover, the ATL chemical fire remains a stark reminder of the delicate balance between industrial progress and public safety. Beyond the immediate devastation, the event has sparked a broader conversation about the role of chemical plants in modern society and the steps needed to mitigate their risks. From improving safety standards to fostering transparency between companies and communities, the lessons learned from this incident have far-reaching implications. As we delve deeper into the causes, impacts, and solutions surrounding the ATL chemical fire, it becomes clear that this is not just a local issue but a global one that demands attention and action.
Table of Contents
- What Caused the ATL Chemical Fire?
- How Did the ATL Chemical Fire Impact the Community?
- Environmental Consequences of the ATL Chemical Fire
- What Are the Lessons Learned from the ATL Chemical Fire?
- How Can Industries Prevent Future Chemical Fires?
- The Role of Government and Regulations in Chemical Safety
- Community Resilience After the ATL Chemical Fire
- Frequently Asked Questions About the ATL Chemical Fire
What Caused the ATL Chemical Fire?
The ATL chemical fire was not a random or unforeseen event but rather the result of a series of interconnected factors that ultimately led to disaster. Investigators determined that the primary cause of the fire was a malfunction in one of the plant's critical storage tanks, which was holding a highly volatile chemical compound. Over time, corrosion had weakened the tank's structural integrity, making it susceptible to leaks. When the tank finally ruptured, the chemicals inside came into contact with an ignition source, triggering a chain reaction that quickly spiraled out of control.
Beyond the immediate technical failure, human error played a significant role in exacerbating the situation. Reports indicate that routine maintenance checks on the storage tank had been delayed or inadequately performed, allowing the corrosion to go unnoticed. Additionally, safety protocols designed to mitigate the risks of chemical fires were either outdated or not rigorously enforced. Employees on-site were reportedly unaware of the proper emergency procedures, leading to confusion and delays in the initial response. This lack of preparedness allowed the fire to spread unchecked, intensifying its impact.
Read also:Unveiling The Mystery Of Michael Jacksons Iconic Blanket A Deep Dive Into Pop Culture History
Another contributing factor was the plant's location within a densely populated area. While zoning regulations permitted the facility to operate near residential neighborhoods, this decision significantly increased the risks to public safety. The proximity of homes, schools, and businesses meant that the fire's effects were felt far beyond the plant's boundaries. Toxic fumes released during the blaze posed immediate health hazards, while the evacuation process placed additional strain on local resources. The combination of technical failure, human oversight, and poor planning underscores the complexity of the ATL chemical fire and highlights the need for comprehensive reforms in industrial safety practices.
How Did the ATL Chemical Fire Impact the Community?
The ATL chemical fire left an indelible mark on the surrounding community, affecting residents in profound and multifaceted ways. The immediate aftermath of the disaster saw widespread panic as thousands of people were forced to evacuate their homes. Emergency shelters were quickly established, but the sudden displacement caused significant emotional and psychological stress for many families. The uncertainty surrounding the duration of the evacuation and the potential long-term effects of the fire added to the community's anxiety, creating a sense of vulnerability that lingered long after the flames were extinguished.
Health Concerns
One of the most pressing issues stemming from the ATL chemical fire was the impact on public health. Toxic fumes released during the blaze contained hazardous chemicals that posed serious risks to respiratory health. Residents reported symptoms such as difficulty breathing, headaches, and nausea, prompting local health authorities to issue advisories about minimizing exposure. Vulnerable populations, including children, the elderly, and individuals with pre-existing medical conditions, were particularly at risk. Hospitals and clinics in the area experienced a surge in patients seeking treatment for respiratory distress, highlighting the urgent need for medical intervention and ongoing monitoring.
Economic Disruptions
Beyond the health implications, the ATL chemical fire caused significant economic disruptions for the community. Local businesses, especially those near the plant, were forced to close temporarily, resulting in lost revenue and layoffs. The tourism industry, a key economic driver in the region, also suffered as visitors canceled trips due to safety concerns. Farmers in the surrounding areas faced challenges as well, with fears of chemical contamination affecting crops and livestock. The cumulative financial toll of the disaster placed additional strain on an already struggling community, underscoring the need for economic recovery initiatives and support systems to help residents rebuild their lives.
Environmental Consequences of the ATL Chemical Fire
The environmental fallout from the ATL chemical fire was both immediate and long-lasting, with far-reaching consequences for the surrounding ecosystem. As the fire raged, toxic chemicals were released into the air, contaminating the atmosphere and posing risks to both human and animal life. The thick plumes of smoke carried hazardous particles over vast distances, affecting air quality in neighboring regions. This widespread pollution raised concerns about the potential for acid rain and its impact on soil and water sources, further complicating recovery efforts.
In addition to air contamination, the fire also had a devastating effect on local water systems. Runoff from firefighting efforts carried chemical residues into nearby rivers and streams, threatening aquatic life and contaminating drinking water supplies. Fish and other aquatic organisms were particularly vulnerable, with reports of mass die-offs in affected areas. The contamination of water sources not only disrupted local ecosystems but also created challenges for communities relying on these resources for agriculture and daily use. Cleanup efforts were initiated to mitigate the damage, but the long-term effects on biodiversity and water quality remain uncertain.
Read also:Kylie Jenner Bikini Pictures A Complete Guide To Her Iconic Beach Looks
The soil in and around the chemical plant also bore the brunt of the disaster. Toxic substances seeped into the ground, rendering large areas unusable for agriculture or development. Farmers in the vicinity faced significant losses as crops became unsafe for consumption, and livestock were exposed to contaminated grazing areas. The soil contamination also raised questions about the potential for long-term ecological damage, as chemicals could persist in the environment for years. Efforts to remediate the affected land are ongoing, but the process is both costly and time-consuming, highlighting the need for sustainable practices to prevent similar environmental disasters in the future.
What Are the Lessons Learned from the ATL Chemical Fire?
The ATL chemical fire serves as a sobering reminder of the critical importance of industrial safety and the need for continuous improvement in risk management practices. One of the most significant lessons is the necessity of proactive maintenance and regular inspections to prevent equipment failures. The corrosion of the storage tank that led to the fire could have been identified and addressed through routine checks, underscoring the importance of adhering to maintenance schedules. Industries must prioritize these practices to ensure the integrity of their facilities and minimize the risk of catastrophic events.
Another key takeaway is the importance of robust safety protocols and employee training. The confusion and delays during the initial response to the ATL chemical fire highlight the gaps in emergency preparedness. Employees must be thoroughly trained in safety procedures and equipped with the knowledge to act swiftly and effectively in crisis situations. Regular drills and simulations can help reinforce these skills, ensuring that workers are prepared to respond to emergencies without hesitation. Additionally, safety protocols should be regularly updated to reflect advancements in technology and industry best practices, ensuring they remain effective and relevant.
Finally, the disaster underscores the need for improved communication and collaboration between chemical plants and the communities they serve. The proximity of the ATL facility to residential areas amplified the risks and consequences of the fire, emphasizing the importance of transparent zoning and land-use policies. Companies must engage with local stakeholders to address concerns and develop strategies for minimizing risks. This includes sharing information about potential hazards, emergency response plans, and ongoing safety initiatives. By fostering trust and cooperation, industries can work alongside communities to create safer and more resilient environments for everyone.
How Can Industries Prevent Future Chemical Fires?
Preventing future chemical fires requires a multifaceted approach that combines technological advancements, regulatory compliance, and a culture of safety. One of the most effective strategies is the implementation of advanced monitoring systems that can detect potential hazards before they escalate. Technologies such as real-time sensors and predictive analytics can provide early warnings about equipment malfunctions, leaks, or abnormal conditions. By integrating these systems into daily operations, industries can identify and address risks proactively, reducing the likelihood of catastrophic events like the ATL chemical fire.
Regulatory compliance also plays a crucial role in preventing chemical fires. Governments and industry bodies must establish and enforce stringent safety standards that leave no room for compromise. This includes mandating regular inspections, requiring the use of fire-resistant materials, and setting limits on the storage of hazardous substances. Companies should also be incentivized to exceed minimum compliance requirements by adopting best practices and investing in cutting-edge safety technologies. Penalties for non-compliance must be severe enough to deter negligence, ensuring that safety remains a top priority for all stakeholders.
Equally important is fostering a culture of safety within organizations. Leadership must prioritize safety at every level, from the boardroom to the factory floor. Employees should be encouraged to report potential hazards without fear of reprisal, and safety training should be an ongoing process rather than a one-time event. Regular audits and reviews can help identify areas for improvement, while open communication channels can ensure that lessons learned from past incidents are shared and implemented. By embedding safety into the core values of an organization, industries can create an environment where chemical fires are far less likely to occur.
The Role of Government and Regulations in Chemical Safety
Government oversight and regulatory frameworks are essential pillars in ensuring chemical safety and preventing disasters like the ATL chemical fire. At the federal, state, and local levels, governments play a critical role in setting standards, enforcing compliance, and holding companies accountable for their actions. Regulatory agencies, such as the Environmental Protection Agency (EPA) and the Occupational Safety and Health Administration (OSHA), are tasked with monitoring chemical plants and ensuring they adhere to safety protocols. These agencies conduct inspections, issue permits, and impose penalties for violations, creating a system of checks and balances that helps mitigate risks.
Legislation is another key component of chemical safety. Laws such as the Clean Air Act and the Emergency Planning and Community Right-to-Know Act (EPCRA) provide a legal framework for managing hazardous substances and protecting public health. These laws require companies to disclose information about the chemicals they use, develop emergency response plans, and engage with local communities. By mandating transparency and accountability, such regulations empower residents to make informed decisions and hold companies responsible for their environmental and safety practices. However, the effectiveness of these laws depends on consistent enforcement and updates to reflect emerging risks and technological advancements.
Despite the existence of robust regulations, challenges remain in ensuring full compliance and addressing gaps in oversight. Limited resources, bureaucratic inefficiencies, and political pressures can hinder the ability of regulatory agencies to perform their duties effectively. Additionally, some companies may prioritize profits over safety, exploiting loopholes or resisting stricter regulations. To address these issues, governments must allocate adequate funding for enforcement, streamline processes to improve efficiency, and collaborate with industry leaders to develop innovative solutions. By strengthening the role of government and regulations, we can create a safer and more sustainable future for chemical industries and the communities they impact.
Community Resilience After the ATL Chemical Fire
In the wake of the
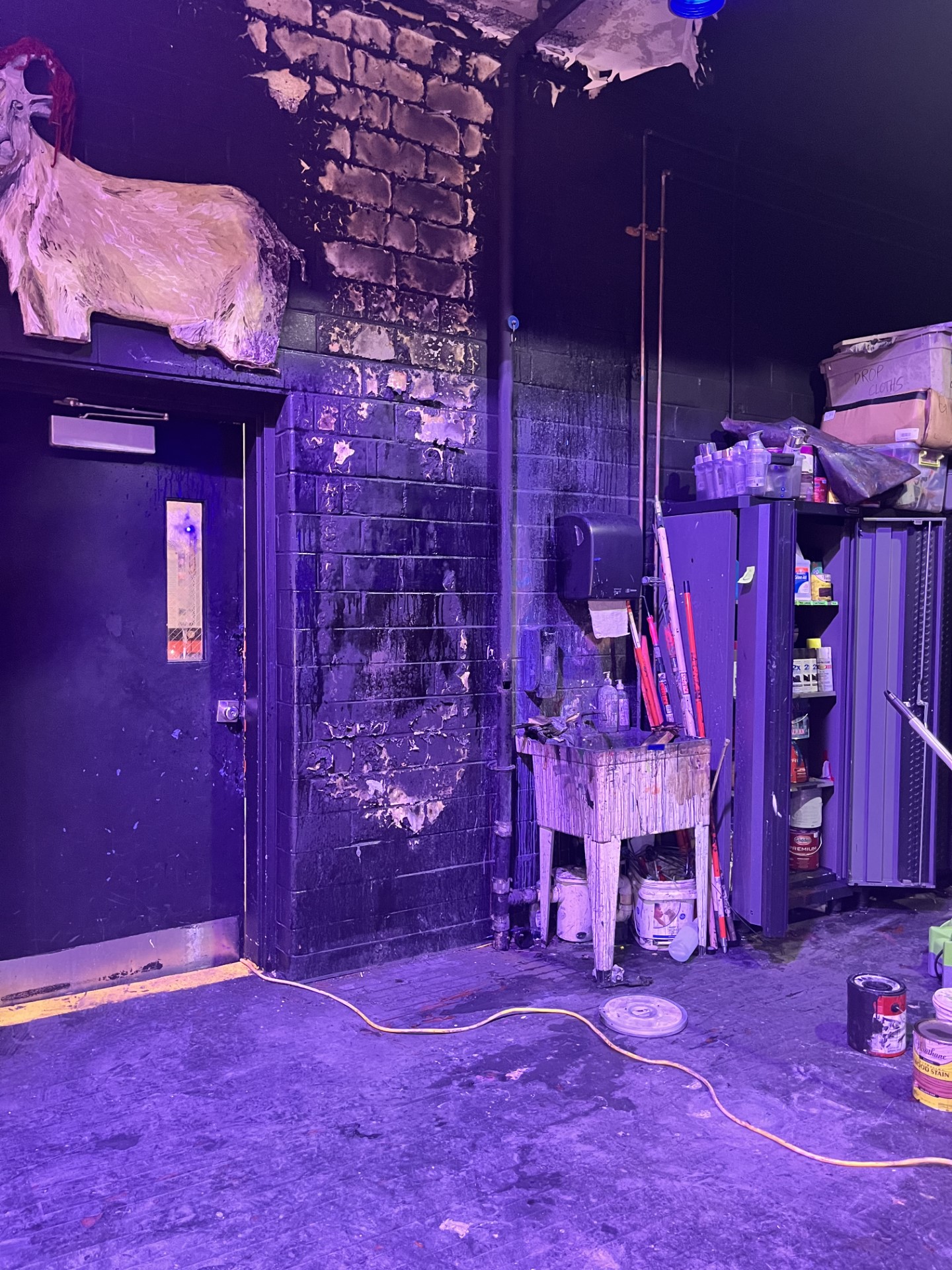
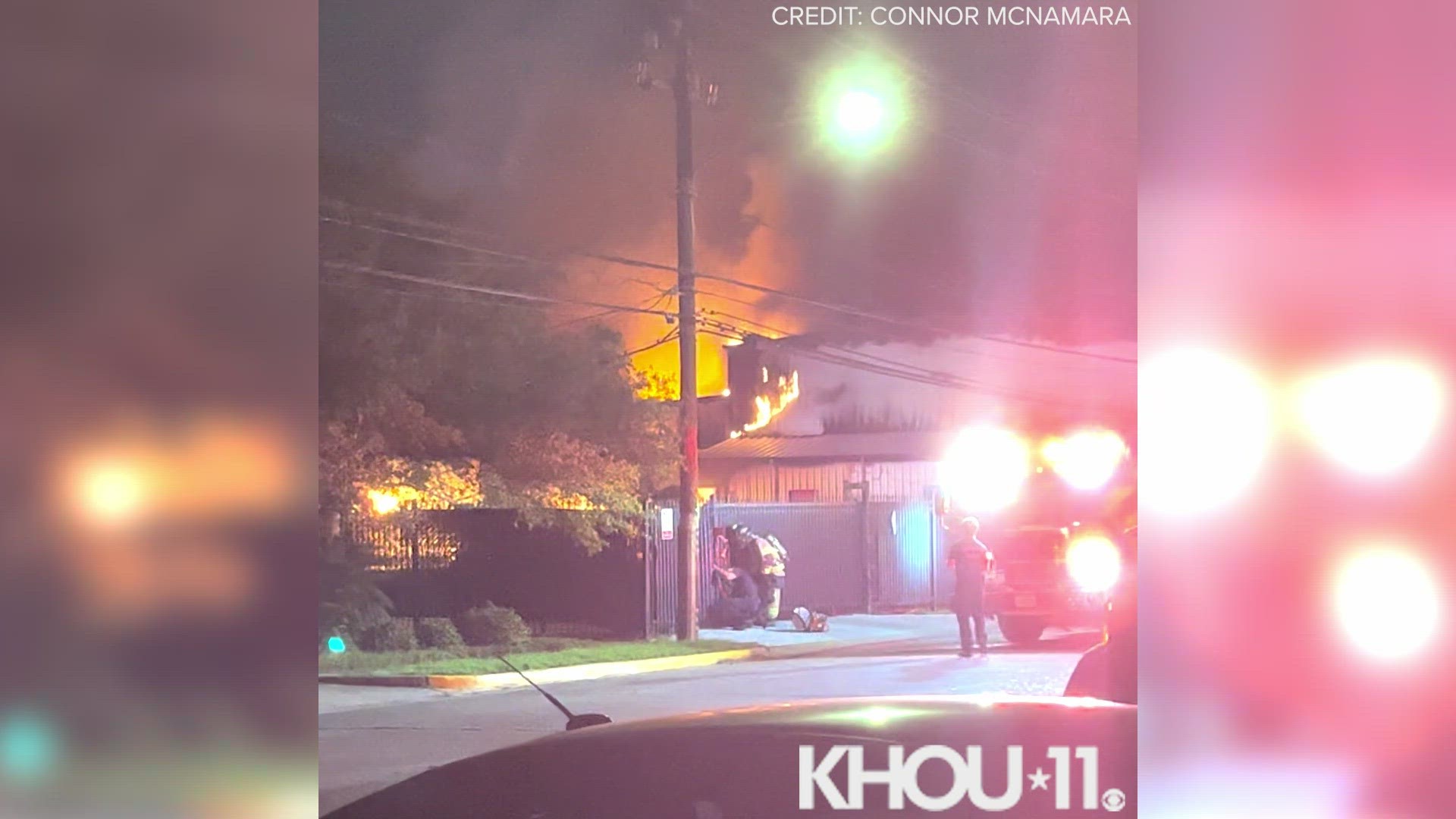