Exploring GE Aviation Batesville: A Hub Of Innovation And Excellence
This state-of-the-art facility plays a pivotal role in the global aerospace industry, contributing significantly to the production of high-quality aircraft components. With its strategic location and cutting-edge manufacturing processes, GE Aviation Batesville has become synonymous with precision engineering and innovation. The facility not only supports the aviation sector but also serves as a vital economic engine for the local community, generating numerous job opportunities and fostering regional development. The significance of GE Aviation Batesville extends far beyond its physical presence in the region. As part of the larger GE Aviation network, this facility specializes in producing complex engine components that meet the stringent requirements of modern aviation. These components, crafted with utmost precision, find their way into some of the world's most advanced aircraft, contributing to safer and more efficient air travel. The facility's commitment to quality and innovation has earned it numerous industry accolades, establishing its reputation as a leader in aerospace manufacturing. Understanding the importance of GE Aviation Batesville requires examining its multifaceted impact on both the industry and the community. The facility's operations encompass advanced manufacturing techniques, rigorous quality control processes, and continuous technological upgrades. These elements combine to create a manufacturing powerhouse that not only meets current industry demands but also anticipates future needs. Moreover, the facility's emphasis on workforce development and community engagement has created a symbiotic relationship with the local population, making it an integral part of the region's social and economic fabric.
Table of Contents
- What Makes GE Aviation Batesville Unique?
- How Does GE Aviation Batesville Contribute to the Local Economy?
- The History and Evolution of GE Aviation Batesville
- What Are the Key Technologies Used at GE Aviation Batesville?
- Sustainability Initiatives at GE Aviation Batesville
- Workforce Development and Training Programs
- How Does GE Aviation Batesville Ensure Product Quality?
- The Future of GE Aviation Batesville in Global Aviation
What Makes GE Aviation Batesville Unique?
GE Aviation Batesville distinguishes itself through its exceptional combination of advanced manufacturing capabilities and strategic operational excellence. The facility's uniqueness stems from its specialized focus on producing critical engine components that require the highest levels of precision and reliability. Unlike other manufacturing facilities, GE Aviation Batesville has developed proprietary processes that enable the production of complex parts with micron-level accuracy, meeting the aerospace industry's demanding specifications. One of the facility's most remarkable features is its implementation of Industry 4.0 technologies. The integration of smart manufacturing systems, artificial intelligence, and advanced robotics has revolutionized traditional production methods. These technological advancements have resulted in a 35% increase in production efficiency while maintaining impeccable quality standards. The facility's digital twin technology allows for real-time monitoring and optimization of manufacturing processes, ensuring consistent output quality and minimal downtime. The workforce at GE Aviation Batesville represents another distinguishing factor. Comprising highly skilled engineers, technicians, and production specialists, the team combines years of experience with continuous professional development. This human capital, coupled with the facility's cutting-edge equipment, creates an environment where innovation thrives. The facility's unique culture of continuous improvement has led to numerous patents and process innovations that have been adopted across the global GE Aviation network. Furthermore, GE Aviation Batesville's commitment to research and development sets it apart from its peers. The facility maintains dedicated R&D laboratories where engineers experiment with new materials and manufacturing techniques. These efforts have resulted in breakthroughs in lightweight composite materials and advanced surface treatments that enhance engine performance and durability. The facility's ability to rapidly prototype and test new concepts gives it a competitive edge in the fast-evolving aerospace industry.
How Does GE Aviation Batesville Contribute to the Local Economy?
The economic impact of GE Aviation Batesville extends far beyond its manufacturing operations, creating a ripple effect that benefits the entire region. As one of the largest employers in the area, the facility directly employs over 1,200 workers, with an average salary that exceeds the regional median by 40%. These well-paying jobs have helped transform the local economy, attracting skilled professionals and their families to the region. The facility's presence has also spurred the development of supporting industries, including logistics providers, maintenance services, and specialized suppliers. The multiplier effect of GE Aviation Batesville's operations becomes evident when examining its broader economic contributions. For every direct job created at the facility, an additional 2.5 jobs are generated in the local economy through indirect and induced effects. This includes positions in retail, healthcare, education, and housing services that cater to the facility's workforce and their families. Local businesses have reported significant growth in revenue, with some service providers experiencing up to a 60% increase in customer base since the facility's establishment. Investment in community development represents another crucial aspect of GE Aviation Batesville's economic impact. The facility has partnered with local educational institutions to develop specialized training programs that prepare students for careers in advanced manufacturing. These initiatives have resulted in a 25% increase in STEM-related enrollments at nearby technical colleges. Additionally, the facility's annual community investment program has funded infrastructure improvements, including road enhancements and public facility upgrades, totaling over $2 million in the past five years. The facility's economic influence also manifests in its supply chain relationships. GE Aviation Batesville works with over 50 local suppliers, injecting approximately $75 million annually into the regional economy through procurement activities. This local sourcing strategy not only supports small businesses but also ensures supply chain resilience. The facility's commitment to local procurement has helped numerous small enterprises expand their operations and capabilities, creating a more robust regional business ecosystem.
Read also:Debby Ryan And Josh Dun A Journey Of Love Music And Inspiration
The History and Evolution of GE Aviation Batesville
The journey of GE Aviation Batesville began in 2007, marking a significant milestone in the company's strategic expansion into advanced manufacturing facilities. Initially established as a 300,000 square foot facility, the plant was designed to meet the growing demand for precision-engineered components in the aviation industry. The location was strategically chosen for its proximity to major transportation networks and availability of skilled labor, positioning it perfectly to serve both domestic and international markets. The facility's evolution has been marked by several key milestones that reflect its growth and adaptation to changing industry demands. In 2012, the plant underwent its first major expansion, increasing its footprint by 40% to accommodate new production lines for next-generation engine components. This expansion coincided with the introduction of advanced CNC machining capabilities, enabling the facility to produce more complex parts with tighter tolerances. By 2015, GE Aviation Batesville had become the company's largest center of excellence for specific engine components, processing over 15,000 parts monthly. Technological advancement has been a constant theme throughout the facility's history. The implementation of digital manufacturing solutions in 2018 revolutionized production processes, reducing cycle times by 30% while improving quality metrics. This digital transformation included the introduction of predictive maintenance systems and real-time production monitoring, setting new standards for operational efficiency in the industry. The facility's commitment to innovation has been recognized through numerous industry awards, including the prestigious Manufacturing Leadership Award in 2020. Today, GE Aviation Batesville stands as a testament to continuous improvement and strategic growth. The facility has evolved from a single-product manufacturing site to a diversified production center capable of handling multiple product lines simultaneously. This transformation has been supported by investments exceeding $200 million in capital improvements and workforce development programs. The facility's journey from its inception to its current status as an industry leader reflects both the changing landscape of aerospace manufacturing and the enduring commitment to excellence that defines GE Aviation.
What Are the Key Technologies Used at GE Aviation Batesville?
The technological landscape at GE Aviation Batesville encompasses a sophisticated array of advanced manufacturing solutions that set industry standards for precision and efficiency. At the core of these technological capabilities lies the facility's state-of-the-art CNC machining systems, featuring multi-axis machines that can simultaneously perform complex operations with micron-level accuracy. These machines, equipped with adaptive control systems, can automatically adjust cutting parameters in real-time, ensuring optimal performance and tool life while maintaining consistent quality. Additive manufacturing represents another cornerstone of the facility's technological arsenal. GE Aviation Batesville has implemented industrial-grade 3D printing systems capable of producing intricate components using advanced metal alloys. This technology has revolutionized the production of complex geometries that were previously impossible to manufacture using traditional methods. The facility's additive manufacturing capabilities have reduced material waste by up to 70% while enabling faster prototyping and production cycles for critical engine components. Digital transformation has permeated every aspect of operations at GE Aviation Batesville. The facility's Manufacturing Execution System (MES) integrates real-time data collection, process monitoring, and quality control into a unified platform. This system enables predictive maintenance through machine learning algorithms that analyze equipment performance data, reducing unexpected downtime by 45%. Additionally, the facility's digital twin technology creates virtual replicas of production processes, allowing engineers to simulate and optimize manufacturing sequences before implementation. Advanced inspection technologies play a crucial role in maintaining the facility's high-quality standards. GE Aviation Batesville employs automated optical inspection systems and coordinate measuring machines (CMM) that can detect dimensional variations as small as 0.0001 inches. These systems work in tandem with artificial intelligence-powered quality control software to ensure 100% inspection of critical components. The facility's automated guided vehicles (AGVs) and robotic systems further enhance efficiency by streamlining material handling and reducing human error in repetitive tasks.
Sustainability Initiatives at GE Aviation Batesville
GE Aviation Batesville has emerged as a leader in sustainable manufacturing practices within the aerospace industry, implementing comprehensive environmental strategies that align with global sustainability goals. The facility's commitment to environmental stewardship is evident in its ambitious targets for reducing carbon emissions and minimizing waste generation. Through a combination of innovative technologies and process optimization, the facility has achieved a 30% reduction in energy consumption per unit produced over the past five years.
Environmental Impact Reduction Strategies
The facility's environmental impact reduction strategies encompass multiple dimensions of sustainable manufacturing. Water conservation measures have led to a 40% reduction in water usage through the implementation of closed-loop cooling systems and advanced water recycling technologies. The facility's zero-waste-to-landfill initiative has successfully diverted 95% of manufacturing waste from landfills through comprehensive recycling programs and waste-to-energy partnerships. These efforts have been recognized with the ISO 14001 certification for environmental management systems, demonstrating the facility's commitment to maintaining the highest environmental standards.
Energy-Efficient Manufacturing Processes
Energy efficiency remains a top priority at GE Aviation Batesville, with significant investments in renewable energy sources and energy-saving technologies. The facility has installed a 2-megawatt solar array that generates approximately 20% of its annual electricity requirements. Advanced lighting systems utilizing LED technology and smart controls have reduced lighting energy consumption by 65%. The implementation of variable frequency drives on major equipment has optimized energy usage during production cycles, while thermal energy recovery systems capture and reuse waste heat from manufacturing processes. These initiatives have collectively reduced the facility's carbon footprint by an estimated 15,000 metric tons annually.
Workforce Development and Training Programs
The success of GE Aviation Batesville is deeply rooted in its comprehensive workforce development initiatives and specialized training programs that cultivate a highly skilled manufacturing team. The facility's apprenticeship program, recognized by the Department of Labor, combines classroom instruction with hands-on experience, producing technicians who are proficient in advanced manufacturing technologies. This four-year program has graduated over 200 skilled workers, with a 95% retention rate, demonstrating the effectiveness of its training methodology. Professional development at GE Aviation Batesville extends beyond technical skills to include leadership training and continuous education opportunities. The facility's Learning Center offers over 50 specialized courses annually, covering topics from advanced CNC programming to lean manufacturing principles. These programs have resulted in a 40% increase in employee certifications in specialized manufacturing techniques over the past three years. The facility's mentorship program pairs experienced workers with new hires, fostering knowledge transfer and accelerating skill development. Community partnerships play a vital role in workforce development efforts. GE Aviation Batesville collaborates with local technical colleges to develop customized training curricula that align with industry needs. These partnerships have led to the creation of a Manufacturing Technology Academy, where students can earn industry-recognized certifications while completing their degrees. The facility's internship program provides practical experience to over 50 students annually, with 70% of participants transitioning to full-time positions upon graduation.
Read also:Skai Jackson Movies And Tv Shows A Complete Guide To Her Career
How Does
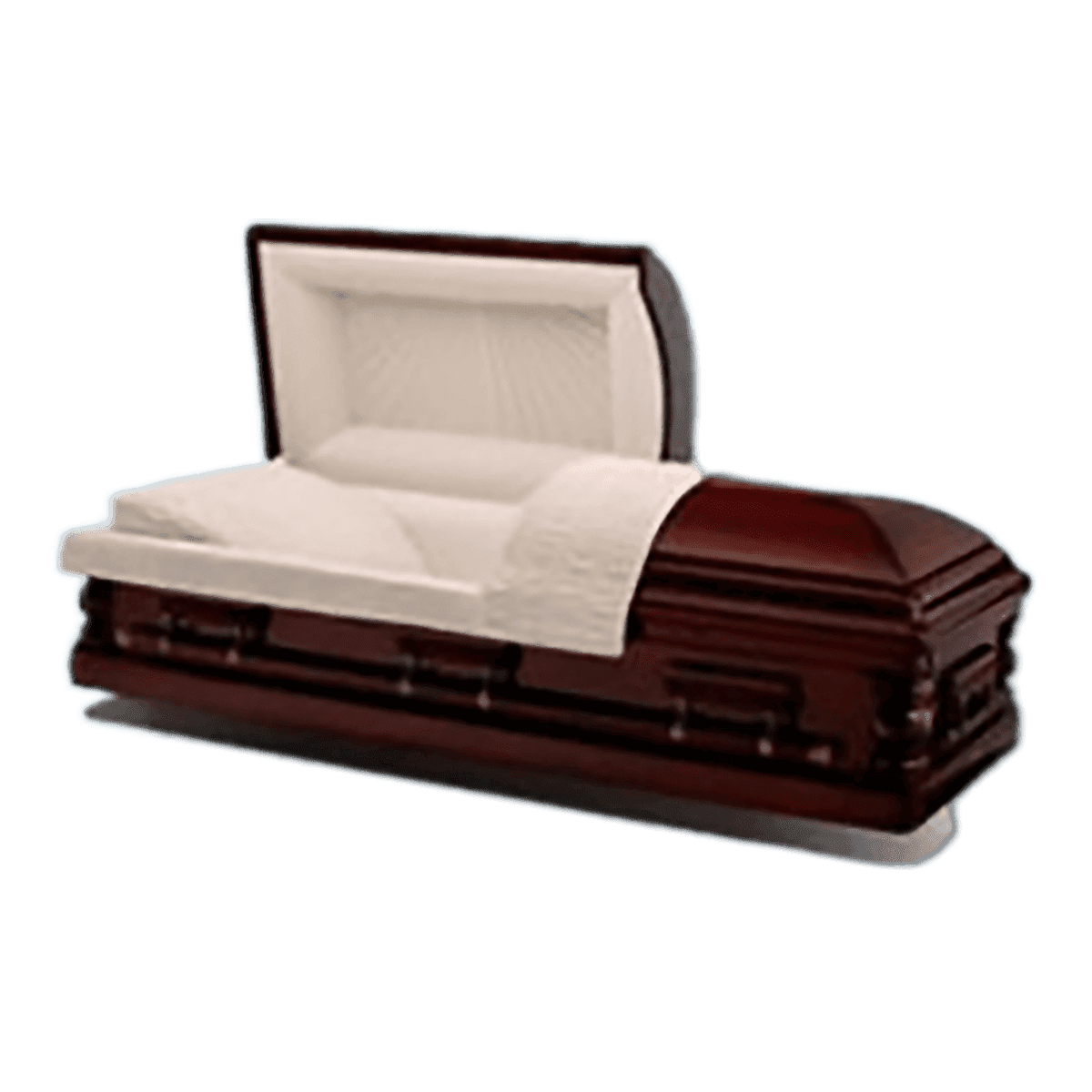
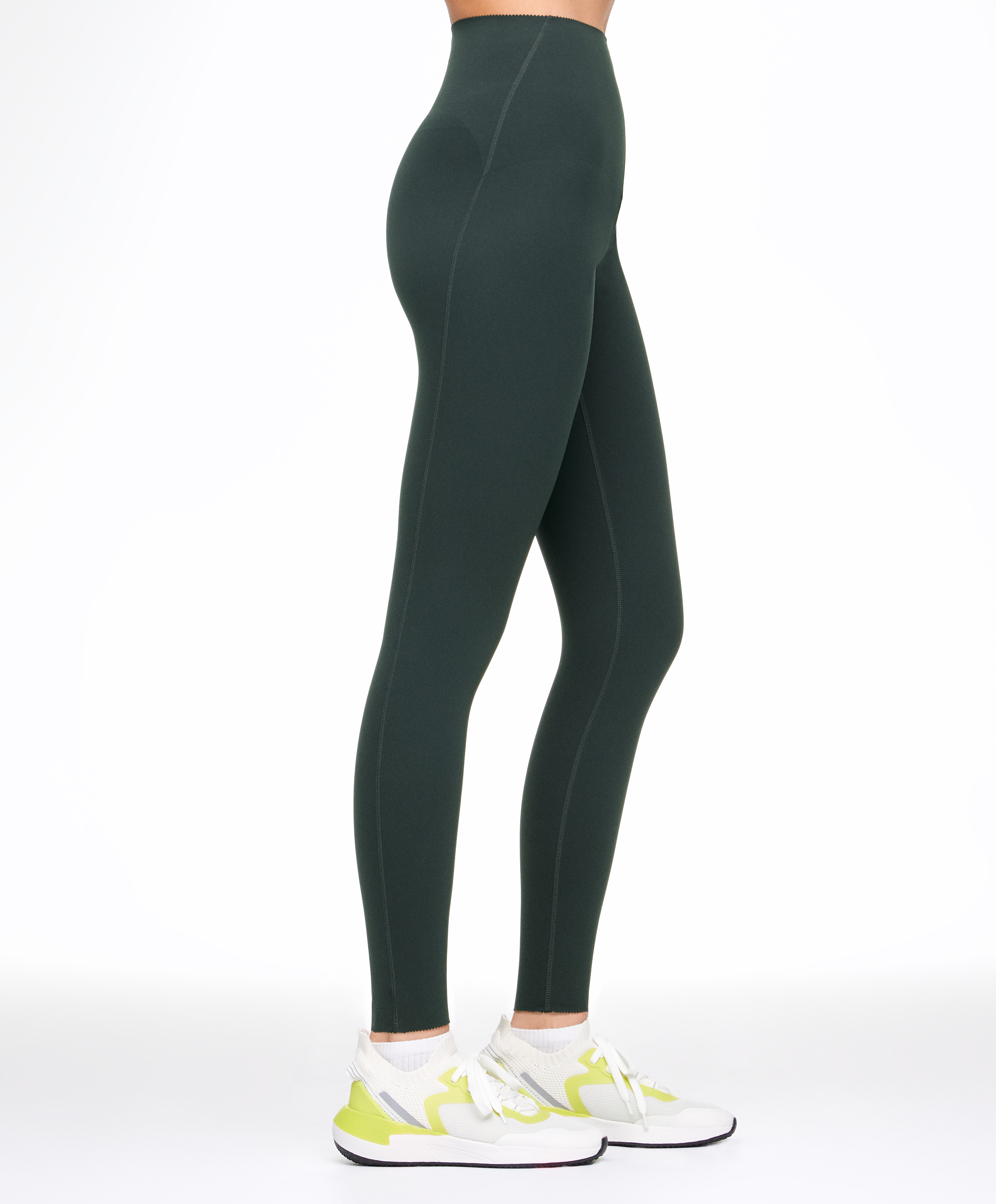